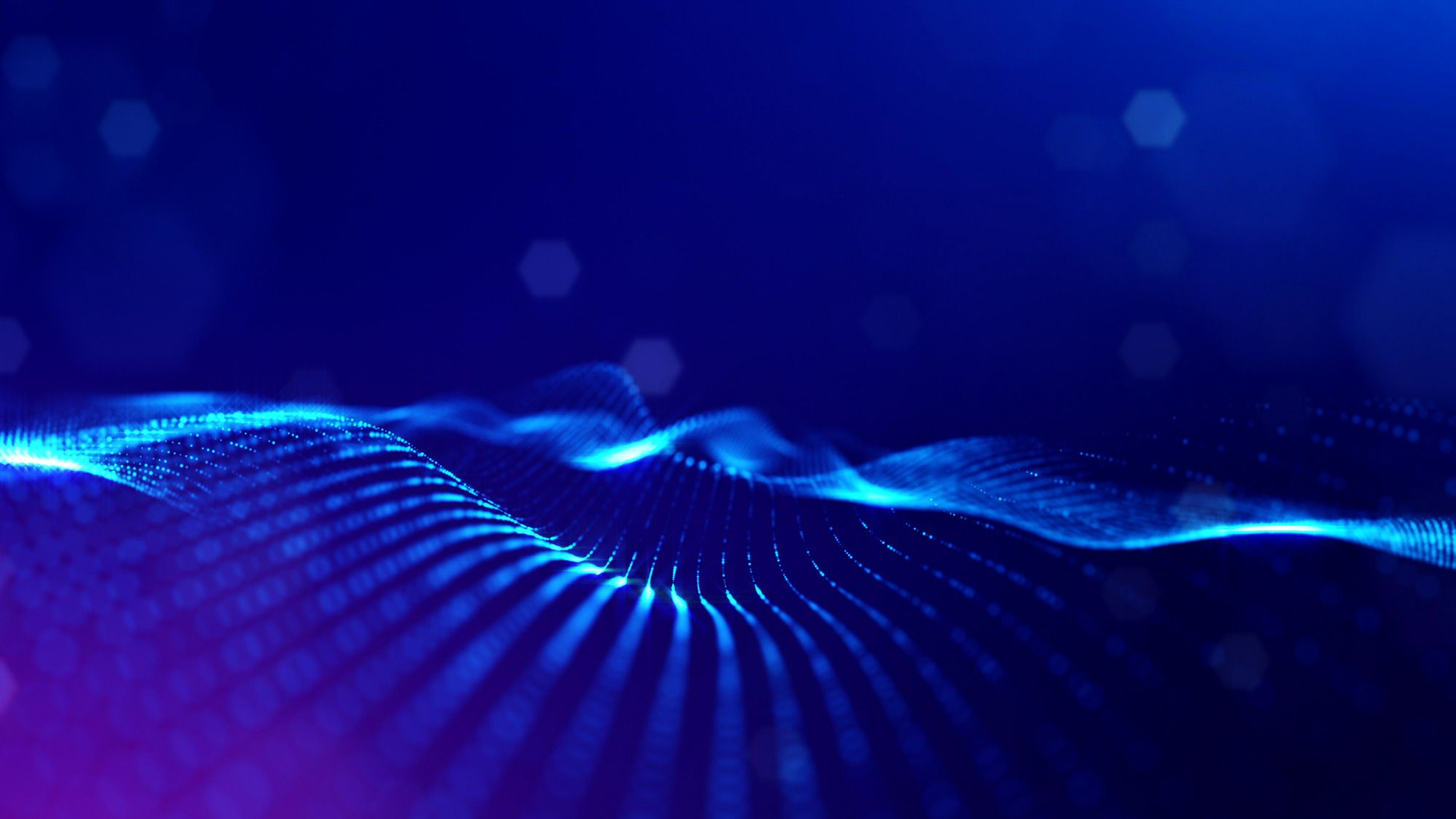
Past Voucher Award Recipient
Westinghouse Electric Co.
partnered with
Oak Ridge National Laboratory
Nuclear Material Holdup Modeling and Measurement Campaign for the Columbia Fuel Fabrication Facility,
NE-19-18711
YEAR AWARDED: FY-2019
TOTAL PROJECT VALUE: $625k (DOE: $500k; Westinghouse: $125k)
STATUS: Completed
PRINCIPAL LAB INVESTIGATORS: Philip Gibbs (ORNL), Jeff Coleman (WEC)
DESCRIPTION: In 2016, the Westinghouse Electric Company Columbia Fuel Fabrication Facility (CFFF) discovered an inadvertent, large accumulation of uranium-bearing materials in a rooftop ventilation scrubber system. The Nuclear Regulatory Commission was notified, and a major extent-of-condition and a root cause analysis were conducted. The main CFFF operations were halted for months while these activities were ongoing. Large quantities of uranium were found in in-service and out-of-service ventilation systems across the plant. Fuel delivery schedules were challenged nearly to the point of failure. Based on this event, regulators all over the world ordered processing facilities to inspect ventilation systems and other equipment and issued notices, reports, orders, and violations based on subsequent discoveries.
IMPACT: An attempt to perform in-situ non-destructive assay on other relatively low SNM content ventilation systems with HEPA filters had met with some success through careful statistical analysis of extensive cleanout data used for a one-time calibration. However, a similar technique for larger process ventilation system cartridge filter banks with high holdup were not similarly developed due to multiple technical factors. These factors included not only the background around the filter banks, but also the geometry and large amounts of material which made them challenging to model. The current method for holdup estimation involves cleanout and filter disassembly, which poses multiple safety hazards to Westinghouse personnel.
BENEFIT: Westinghouse Electric Company and Oak Ridge National Laboratory have designed and performed an experiment to develop a non-destructive assay measurement method that addressed the challenges of the volumetric deposits within the large ventilation system housings. This method, involving modeling and NDA measurements, allow the holdup accumulations to be better monitored and estimated, which additionally precluded the need for filter disassembly, greatly reducing or eliminating the need for cleanouts.
SIGNIFICANT CONCLUSIONS: Volumetric non-destructive assay models created for one type of system (specific geometry that includes two cartridge filters per row) were used to accurately predict the cleanout values of another like-kind system. Thus, this model works for the systems in this area processing this specific material type.
NEXT STEPS: CFFF will build a certified reference non-destructive assay standard similar to the one used in the ORNL model development. It will use similar calibration techniques to parameterize the templatized model provided by ORNL to develop non-destructive assay measurement methods for all similarly configured ventilation systems (columns of two cartridge filters, two filters deep) across the plant—various processes with varying material compositions. The vast majority of these cartridge filter banks will be modeled and calibrated by the next CFFF inventory. This leaves only a few filter banks of different geometry for future modeling. More research and development work will be required to measure these few remaining systems with multiple columns of cartridge filters in larger arrays.