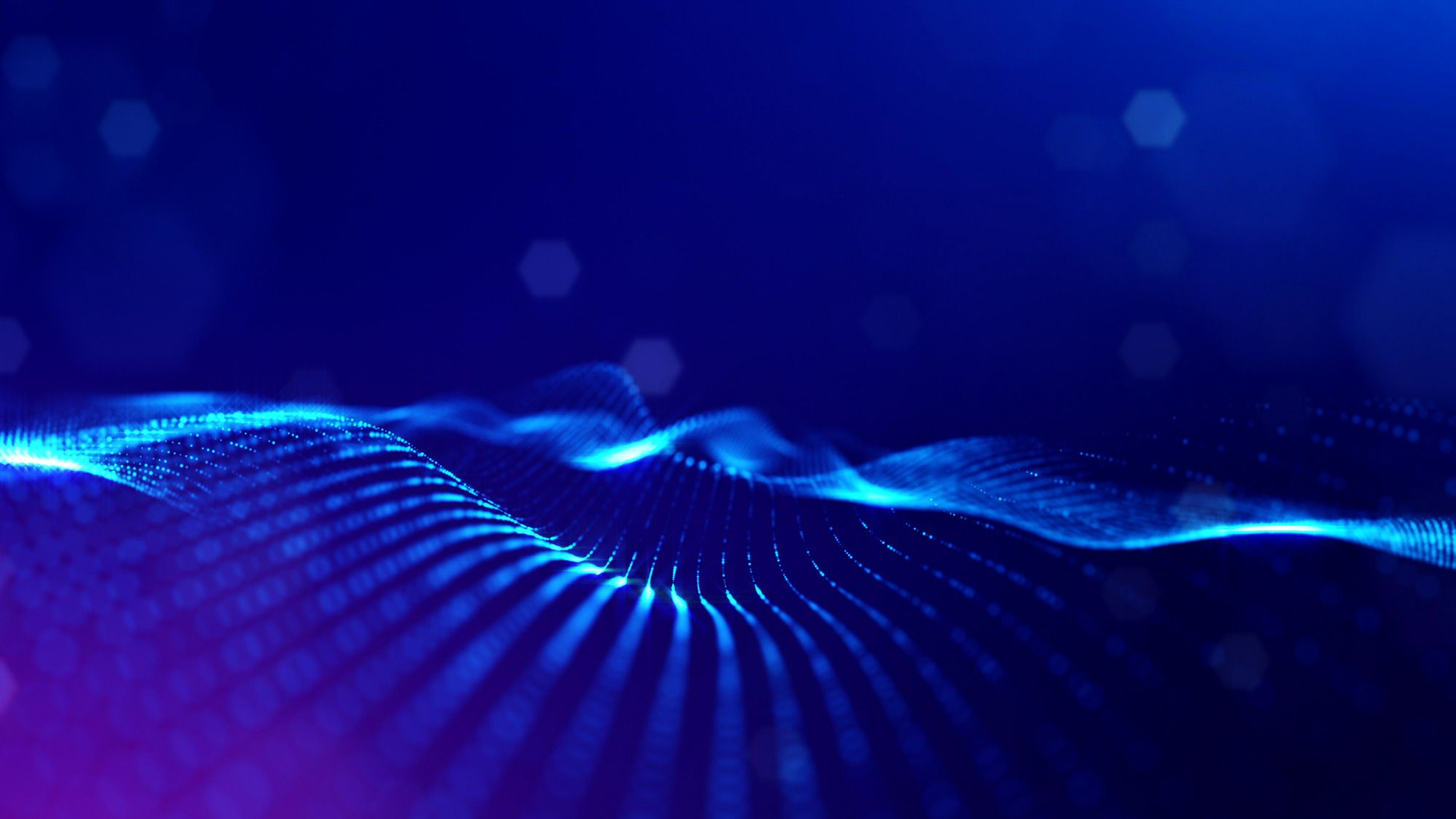
Past Voucher Award Recipient
Westinghouse Electric Company, LLC.
partnered with
Oak Ridge National Laboratory
Multiphysics Design Optimization and Additive
Manufacturing of Nuclear Components, NE-21-25129
YEAR AWARDED: FY-2021
TOTAL PROJECT VALUE: $500,000 ($400,000 DOE, $100,000 Westinghouse)
STATUS: Completed
PRINCIPAL LAB INVESTIGATORS: Nate See (ORNL), Zeses Karoutas (Westinghouse)
DESCRIPTION: In this project, Westinghouse Electric Company (WEC) requested the help of Oak Ridge National Laboratory (ORNL) in the creation of a new design tool set for developing novel ideas outside the normal scope of traditional nuclear fuel and reactor design. Specifically, they focused on redesigning a hexahedral spacer grid to perform beyond the WEC set objectives. The researchers used Siemens HEEDS, a design space exploration and parametric optimization software, to adjust the native CAD of the spacer grid with geometry that is additively manufacturable.
BENEFIT: A design pathway that empowers nuclear design engineers to creatively explore novel design concepts using modern computing resources and design techniques to leverage additive manufacturing (AM) printing capabilities provides innovation for current light-water reactors and the entire advanced reactor space.
IMPACT: Combining multiple design optimization methodologies with the forethought to implement AM technologies to explore beyond the boundaries of conventional design processes will prompt rapid modernization of the aging nuclear fuel and reactor design space. Furthermore, it will accelerate the processes, which has traditionally taken years and involved large research teams.
SIGNIFICANT CONCLUSIONS: The ORNL team demonstrated that the HEEDS optimization routine can independently develop a design that meets Westinghouse’s design goals. Although these designs were at a low technology readiness level, their demonstration confirmed the team’s ability to create novel advanced nuclear concepts.
NEXT STEPS: Focused on a current spacer grid design that can allow for a reduced hydraulic pressure drop and reduced material usage, Westinghouse sought to think outside the box by removing conventional thought process limitations. The Oak Ridge National Laboratory team took two different pathways. The first pathway used Siemens NX Topological optimization and engineering adjustments based on WEC’s design specifications and common aerodynamic design principles. The second pathway included development of a parametric design optimization routine within Siemens HEEDS to create and evaluate potential designs from the NX Topology add-in. Although the programs performed nearly the same in reducing the overall mass needed, the human intervention of modern aerodynamic design outperformed the HEEDS design hydraulically, reducing the hydraulic pressure loss by a factor of 4. It is recommended that WEC continue enhancing the HEEDS routine to help bring the design routine closer to the human engineering intervention. Ultimately, the designs provided should be considered a starting point from which experienced engineers can further evaluate and adjust as needed.