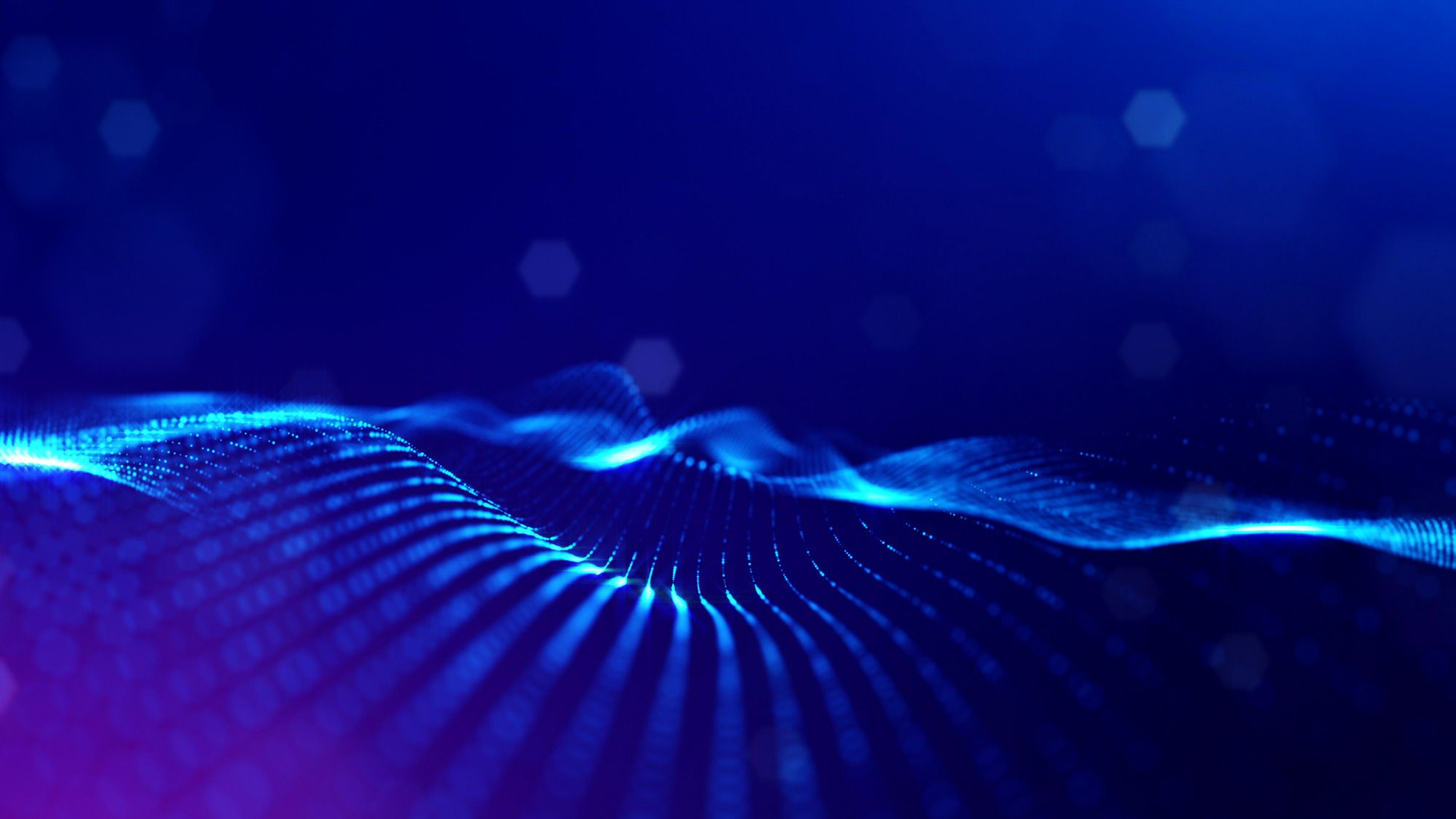
Past Voucher Award Recipient
Lightbridge Corporation
partnered with
Pacific Northwest National Laboratory
Development of Casting Techniques for ẟ-phase Uranium-Zirconium Alloys, NE-21-25980
YEAR AWARDED: FY-2021
TOTAL PROJECT VALUE: $663,500
STATUS: Completed
PRINCIPAL LAB INVESTIGATORS: Zach (PNNL), Jim Fornof (Lightbridge)
DESCRIPTION: Lightbridge Corporation, based in Reston, Va., is a nuclear fuel technology development company whose mission is “to develop innovative next generation nuclear fuel technologies for current and future reactors, which significantly enhance the economics and safety of nuclear power.” Casting δ-phase U-Zr alloys, as compared to unalloyed and lightly alloyed uranium, requires higher temperatures. Because carbon, oxygen, and nitrogen content increases as a function of casting temperature and crucible coating, this increases the likelihood of a detrimental reaction between the alloy melt and crucible material. With higher impurity contents, the microstructural stability of the alloy can be compromised. The casting, processing, and shipping of HALEU alloys, like those being developed by Lightbridge, require the ability to experiment with higher temperatures in a facility that can perform these functions. The goal of this project was to identify an appropriate casting method (i.e., crucible and coating combination) that results in an acceptable impurity concentration in the as-cast ingot.
BENEFIT: The objective of this project was to determine an acceptable casting process for the Lightbridge δ-phase U-50Zr alloy using a depleted uranium (DU) zirconium alloy in the Radiochemical Processing Laboratory (RPL) at the Pacific Northwest National Laboratory (PNNL). PNNL brings expertise in developing processes for advanced uranium alloy casting and is the fabrication lead for the U.S. High Performance Research Reactor (USHPRR) conversion project.
IMPACT: The work covered by this voucher sought to identify a methodology for successfully casting U-50Zr. Previously reported works used small quantities of U-50Zr, whereas this work investigated a larger lab-scale quantity (~1kg). The success was measured by ability to limit impurity elements such as C, O, N that result in carbide or α-phase stabilization as well as the UZr2 phase purity of the sample. Five castings were carried out using arc melted master alloy feedstock. The methodologies used during arc melting and casting were coupled with analysis of the resulting C, O, N, H impurities, phase characterization and microscopy.
SIGNIFICANT CONCLUSIONS: Overall, the highest success castings were completed with a graphite crucible utilizing a TiC underlayer and Y2O3 overcoat in this work. Once proper coating procedures were established, this combination resulted in two successful castings. The two successful castings had C, O, and N contamination levels low enough that limited carbide and α-phase stabilization while producing the desired δ-UZr2 phase.
NEXT STEPS: Additional casting trials with this casting methodology are recommended to establish statistical significance, understand the success rate associated with these parameters, and optimize the method. Furthermore, future work should involve pouring the melt into a similarly coated mold to allow for a more practical final shape before further processing such as extrusion. In addition, the use of ZrO2 crucibles or other ceramic crucibles of interest needs further investigation.