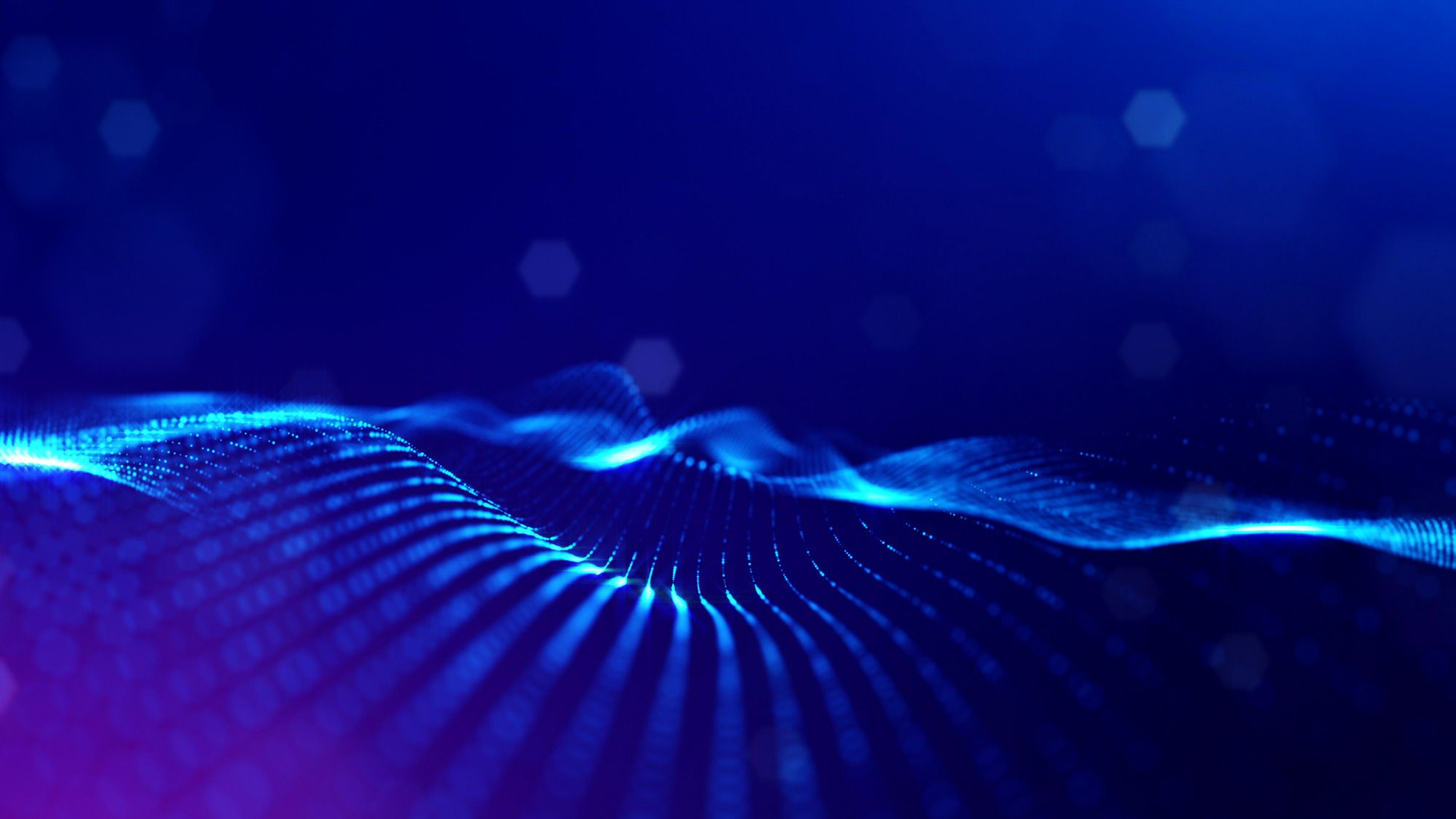
Past Voucher Award Recipient
GSE Systems
partnered with
Idaho National Laboratory
Human Factors Engineering for the Move
to Digital Control Systems, RFA-17-14602
YEAR AWARDED: FY-2017
TOTAL PROJECT VALUE: $150K (DOE funding, $120K, awardee cost share, $30K)
STATUS: Completed
PRINCIPAL LAB INVESTIGATORS: Ron Boring ([email protected])
DESCRIPTION: Existing control rooms in nuclear power plants present a labyrinth of analog indicators and controls. The control boards are configured with one-to-one mappings of sensors to indicators and controls to switches. This arrangement speaks to the analog vintage of the control rooms and omits display and control efficiencies that are possible with newer, digital technologies. As efforts are undertaken to modernize control rooms, the end-state vision is for these legacy control boards to be replaced by distributed control systems that enhance the functionality of the predecessor system. Under this Gateway for Accelerated Innovation in Nuclear voucher, Idaho National Laboratory collaborated with GSE Systems, proprietor of the Generic Pressurized Water Reactor, a full-scope simulator of a three-loop pressurized-water reactor, to develop a simple system that allows control of a plant simulator from a workstation. Called the Task Engine for Job and User Notification (TEJUN, also the Japanese word for “procedure”), the system is a web-based application that allows procedures to be authored in an easy-to-read document format.
BENEFIT: While the TEJUN is meant to be a proof-of-concept for a simplified control room based on computerized procedures, the system also can serve training and research purposes. By minimizing the need for the full-scale real estate of a control room and by eliminating the need for geospatial memory of board layouts, the simulator becomes considerably easier to use, thus reducing training requirements and opening the door for use by student operators in research.
IMPACT: Although research is still ongoing, the team believes the TEJUN computerized procedure system, coupled with the Graphical Augmentation Interface for Yoked Overviews, could greatly simplify control room interfaces and also provide a flexible architecture for GSE Systems and affiliated researchers to use in developing streamlined interfaces for advanced reactor concepts.
LESSONS LEARNED: The approach is scalable. Any procedure can be represented in the computerized procedure system, and any indicator or control modeled within the simulator can be invoked within the procedure.
SIGNIFICANT CONCLUSIONS: Existing plant procedures have evolved over decades of operations and tens of thousands of operator hours of experience. With a new procedure system, it is important to not disregard the value of existing procedures.
NEXT STEPS: We will need to address several outstanding issues to make commercial computerized procedure systems viable. Some of these issues are potentially applicable to other industries and next generation nuclear power plants, but many issues are unique to the modernization of existing light-water reactors, and new tooling is needed to address them in order to gain critical industry and regulatory support. This calls for a computerized procedure support system specifically designed to be flexible in addressing human factors.