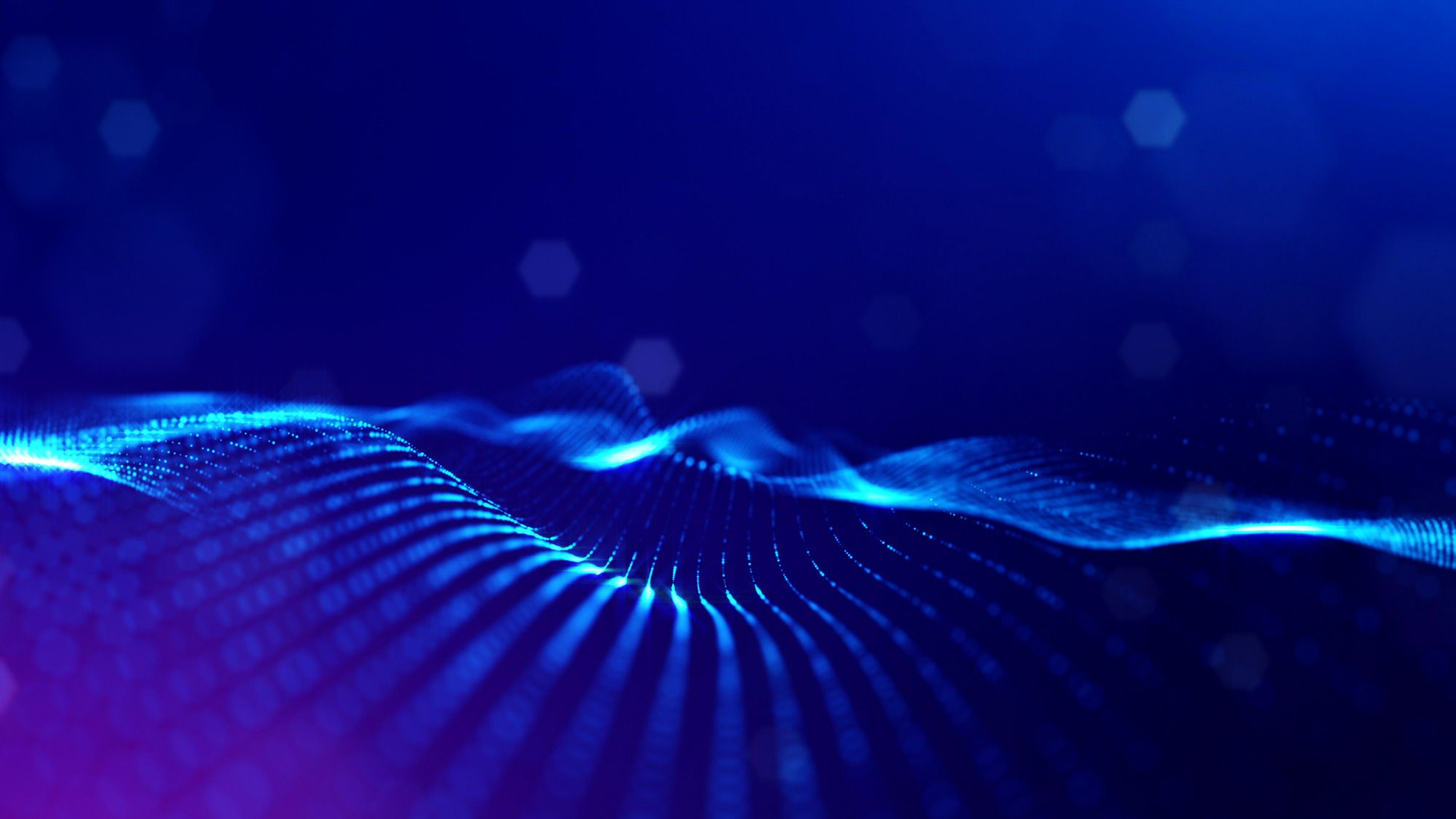
Past Voucher Award Recipient
Creare LLC
partnered with
Idaho National Laboratory
Investigation of Materials for Continuous
Casting of Metallic Nuclear Fuel, GA-16IN020101
YEAR AWARDED: FY-2016
TOTAL PROJECT VALUE: $75K (DOE funding, $60K; awardee cost share, $15K)
STATUS: Completed
PRINCIPAL LAB INVESTIGATORS: Randall Fielding ([email protected])
DESCRIPTION: Creare, LLC, worked with researchers at Idaho National Laboratory (INL) to identify and test initial concepts for coating materials to be used in testing a continuous casting process aimed at reducing the cost of fuel pin production compared with conventional fabrication methods for metal fuel. Some innovative reactor designs use uranium alloy fuel pins with annular geometries that remove sodium from the fuel pin making disposition easier and improving neutron economy. High-volume advanced manufacturing methods are needed to realize these benefits, since it is unlikely that injection casting, the traditional fuel casting technique, is feasible for an annular pin, as the mold would need to be removed from the center of the pin after casting. Under this Gateway for Accelerated Innovation in Nuclear voucher, multilayer coatings for use with a graphite substrate were identified and tested against a fuel alloy. Unique capability provided by INL included use of a mechanically reliable crucible that maintained purity of the fuel material during the casting process as well as expertise in assessing material behavior in nuclear fuel fabrication systems.
BENEFIT: This work provided experience with coating of high temperature alloys (Cu-Ni in this case), the results of which have been used to map out the next evolution of coating technology, a necessary step toward commercialization of the process.
IMPACT: INL was very professional and efficient at establishing a Cooperative Research and Development Agreement with Creare. The company continues to develop a casting process to produce annular metallic fuel pins that meet precise dimensional requirements, minimize post-processing, and reduce waste.
SIGNIFICANT CONCLUSIONS: The team first identified candidate multilayer coatings for use with a graphite substrate. Initial casting trials provided valuable supporting data for hypotheses on coatings and treatments for this system. The work also provided experience with coatings applicable to casting high temperature alloys (Cu-Ni in this case) as a progression from previous experience with lower temperature alloys.
NEXT STEPS: In the next phase of development, advanced precision casting equipment will operate at very high temperatures (1300–1400°C) using a molten metal that more closely models nuclear fuel alloys. The company plans to develop needed equipment to produce the pins, run multiple series of fabrication experiments, and refine the design of the equipment based on the measured dimensions and metallurgical properties of the castings.